Table of contents:
Material Selection Galvanized vs Stainless Steel
Impact of Construction Types on Sling Performance
Testing Procedures for Load Capacity Verification
Maintenance Tips to Extend Service Life
Material Selection Galvanized vs Stainless Steel
Selecting the right material for your heavy-duty wire rope slings is one of the most important decisions in ensuring durability and performance. The two most common options are galvanized and stainless steel. Galvanized wire rope slings offer excellent corrosion resistance and are typically more cost-effective, making them a popular choice for environments prone to occasional moisture but with limited exposure to harsh chemicals or extreme weather. Stainless steel, on the other hand, is inherently rust-proof and resilient, making it ideal for applications exposed to saltwater, chemicals, or consistently humid conditions. While stainless steel may come at a higher upfront cost, its longevity and ability to endure challenging environments often outweigh the initial expense. For operations requiring custom wire rope slings, discussing your environmental factors with a supplier is critical to ensure the best material is selected to meet your specific needs.
Impact of Construction Types on Sling Performance
Wire rope slings come in various constructions, each designed for specific load types and performance characteristics. Single-part slings provide a straightforward design and are often used in simpler lifting applications, while multi-part braided slings offer added flexibility and strength for heavy or irregularly shaped loads. The number of wire strands and the lay pattern also significantly affect performance. A tighter lay, where wires are wound closer together, provides better resistance to abrasion but reduced flexibility, making it suitable for applications with continuous contact against hard surfaces. Conversely, a looser lay improves flexibility and is ideal for scenarios requiring frequent bending around corners or other obstacles. Choosing the right sling construction is essential to optimize load security while ensuring longevity. Custom lifting slings not only cater to the specific physical demands of your project but also enhance the overall safety and reliability of your operations.
Testing Procedures for Load Capacity Verification
One of the most critical stages in ensuring quality in heavy-duty wire rope slings is verifying their load capacity. Rigorous testing procedures help assess the maximum load a sling can safely handle, ensuring compliance with industry standards and mitigating risks during lifting operations. Proof testing is a standard phase where the sling is subjected to predetermined loads to verify performance against its rated capacity. Destructive testing, meanwhile, involves testing the breaking point of a sling to reinforce confidence in its safe working load (SWL). Third-party certifications can boost confidence in compliance, while working with reputable suppliers who perform regular in-house testing is equally important. Before purchasing wire lifting slings for sale, always confirm that they meet the necessary regulatory requirements, undergo frequent capacity testing, and come with quality assurance documentation. An accurate understanding of load capacity not only ensures safety on the job site but also reduces operational inefficiencies caused by unexpected equipment failures.
Maintenance Tips to Extend Service Life
Proper maintenance is key to ensuring the longevity of heavy-duty wire rope slings. Regular inspection for wear and tear, such as broken strands, corrosion, or kinks, should be part of standard operating procedures. When not in active use, slings should be stored in a clean, dry area to reduce risk from environmental factors like moisture or extreme temperatures that could degrade material integrity. Cleaning dirt, grease, or other contaminants from the rope’s surface prevents them from settling into crevices, where they could speed up wear. Additionally, using lubricants specifically designed for wire ropes can prevent internal abrasion and corrosion, thus extending service life. For those using custom lifting slings or working in particularly demanding environments, scheduling professional inspections ensures higher accuracy in detecting potential issues before they escalate. Implementing small, routine maintenance measures pays off through fewer repairs, extended lifespan, and lowered costs in acquiring replacements.
By understanding the importance of material choice, construction type, testing standards, and maintenance, businesses can ensure the reliability and durability of their heavy-duty wire rope slings. These components are the backbone of many industries, and attention to detail in their quality can prevent costly errors and unsafe conditions. For those looking to purchase wire lifting slings for sale or customize lifting slings to fit specific projects, partnering with experienced providers can make all the difference. The efficiency and longevity of your operations often depend on the care and quality measures you invest in today.
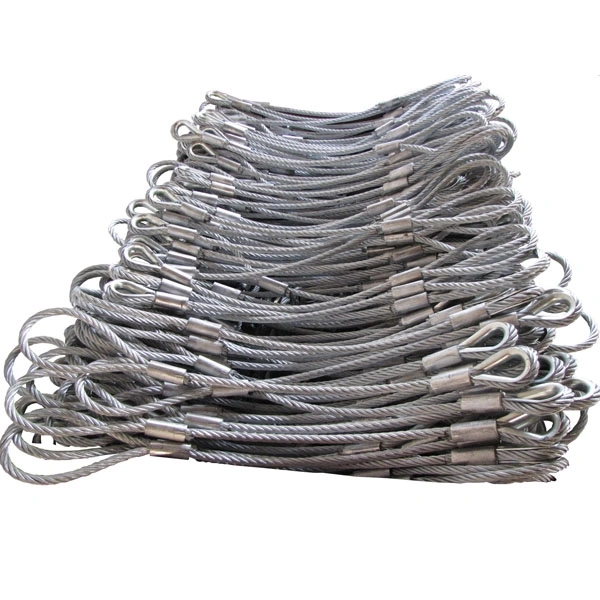
Comments
Post a Comment