Table of contents:
Why Choose Custom CNC Machining Service for Precision Plastic Components
The Advantages of Custom CNC Machining Over Traditional Manufacturing Methods
How Custom CNC Machining Can Enhance Your Plastic Product Designs
Cost-Effective Solutions with Custom CNC Plastic Machining Services
Why Choose Custom CNC Machining Service for Precision Plastic Components
Custom CNC machining service stands apart from conventional manufacturing methods through its unparalleled precision and versatility. CNC precision machining services leverage computer-controlled systems to execute complex cutting operations with microscopic accuracy, ensuring each plastic component meets exact specifications every time. This level of consistency proves invaluable for industries where even minor deviations can result in product failure or safety concerns. The automated nature of CNC systems eliminates human error from the manufacturing equation, while advanced software controls enable manufacturers to achieve tolerances as tight as ±0.001 inches. Furthermore, custom CNC machining accommodates virtually any plastic material, from standard thermoplastics like ABS and polycarbonate to specialized engineering plastics such as PEEK and POM. This material flexibility allows designers to select the optimal plastic for their specific application without compromising on manufacturing capabilities. The process also excels at creating complex geometries that would be impossible with traditional manufacturing methods, including intricate internal features, precise threading, and detailed surface textures that enhance both functionality and aesthetics.
The Advantages of Custom CNC Machining Over Traditional Manufacturing Methods
Traditional plastic manufacturing methods, including injection molding and thermoforming, require substantial upfront investments in tooling and molds. Custom CNC machining eliminates these barriers by working directly from digital designs, making it particularly attractive for prototyping and low-to-medium volume production runs. CNC plastic machining offers rapid turnaround times that traditional methods cannot match—complex parts can be produced within days rather than weeks or months required for mold creation. The process also provides unmatched design flexibility, allowing engineers to incorporate features like undercuts, complex geometries, and intricate internal channels that would be impossible or extremely costly with conventional techniques. Quality control represents another significant advantage, as CNC systems maintain consistent performance throughout production runs without the wear-related quality degradation common in traditional tooling.
How Custom CNC Machining Can Enhance Your Plastic Product Designs
Precision plastic machining opens new possibilities for product designers who previously faced limitations imposed by traditional manufacturing constraints. The technology enables the creation of highly detailed features such as precise mounting points, intricate cooling channels, and complex internal structures that improve product functionality. CNC plastic machining also allows for superior surface finishes that eliminate the need for secondary operations, reducing overall production time and costs. Designers can incorporate features like precise fits and tolerances that ensure perfect assembly with other components, critical for applications in electronics, medical devices, and aerospace components. The ability to machine multiple materials within a single production run enables the creation of multi-material assemblies without additional assembly steps.
Cost-Effective Solutions with Custom CNC Plastic Machining Services
Despite initial perceptions about cost, custom CNC plastic machining services deliver exceptional value through multiple cost-saving mechanisms. The elimination of tooling costs makes CNC machining highly economical for prototype development and low-volume production runs where traditional methods would be prohibitively expensive. The superior precision of CNC machining reduces scrap rates and rework requirements, directly impacting the bottom line through improved material utilization. Additionally, the ability to produce finished parts in a single operation eliminates secondary machining costs and reduces handling time, further improving overall economics. The speed of CNC production allows for faster time-to-market, providing competitive advantages that translate into revenue benefits that far exceed manufacturing cost differences.
Precision plastic machining plays a pivotal role in meeting the demands of modern industries, offering unmatched accuracy, versatility, and efficiency. By partnering with a trusted CNC machining provider, businesses can ensure the highest quality production while achieving their technical and operational goals. Investing in precision manufacturing is not just about meeting immediate project needs—it's about building a foundation for long-term growth, innovation, and success in an increasingly competitive marketplace.
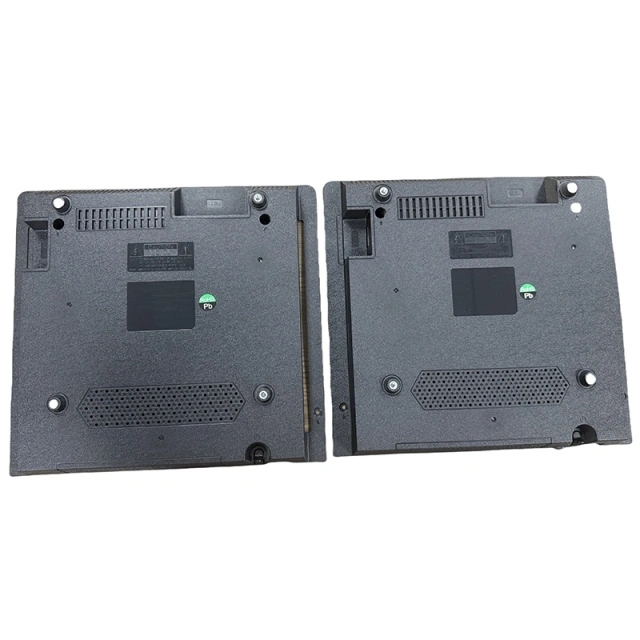
Comments
Post a Comment